Injector – micro-injection taken to extremes
- Published on the December 8, 2024
When it comes to micro-injection, Injector’s expertise puts this SME, with just under 15 employees, head and shoulders above the rest. That expertise is underpinned by an incredible mastery of its tools.
“Making a part injectable that originally wasn’t” is how Michel Hoff, the man responsible for business development at the company, sums up the process. Hoff is passionate and inspiring, and his enthusiasm is contagious. His words exude both in-depth technical knowledge and a desire to share.
The remarkable rehaut of a famous watch
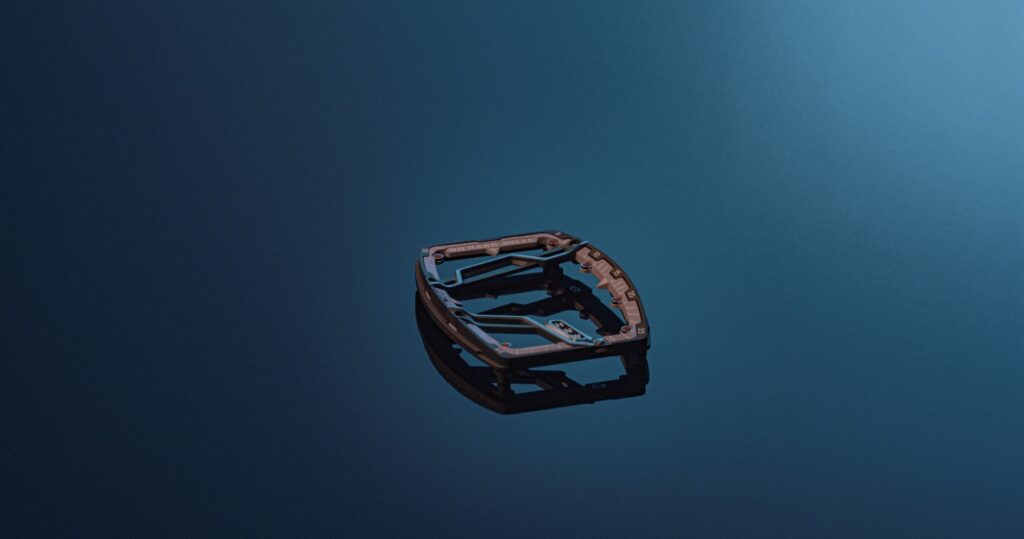
The firm’s high-end creations include this rehaut (flange), available in multiple shades. With its ultra-lightness, solidity and reliability, it represents the holy grail for one of today’s most sought-after watch brands. The brief for the watch – the first women’s sports watch with a record-low weight of 36 grams – was so draconian that it ruled out any use of machinable materials. Only micro-injection could meet the customer’s demanding expectations.
The result ? The firm has pulled off the seemingly impossible with an amazing tour de force: as well as mastering the technology and constraints of micro-injection and of tool design, it had to invent a ‘mould’ capable of injecting from six injection points distributed at different locations around the edge of the part. And not only that but at a pressure of up to 1,500 bars, using presses with a closing force of 35 tonnes! This feat of miniaturisation avoids a number of pitfalls, linked to the variable nature of the pigments used for each shade required, as well as the aesthetic complexity of the component. A key part for absorbing play between the middle and the dial, the rehaut has to be completely flat, and its rigidity is vital for subsequent manual operations.
Finishing touches by the human hand
But at the end of the process, human dexterity makes the final tweaks, erasing any flow lines, shrinkage or burrs, and it is the human hand that takes care of the SLN filling and fine pad printing. It is also important to remember that, initially, the injection took place around micro-feet, thanks to a mould that specifically incorporated them.
Words cannot describe and the human eye struggles to make out the rehaut’s subtle detailing, so let us turn back for a moment to Michel Hoff and find out about the latest developments with itr2®, Injector’s innovative material involving workpieces filled with carbon or glass fibre nanoparticles. This material can be machined, and indeed the company has a dedicated machining and finishing unit in-house.
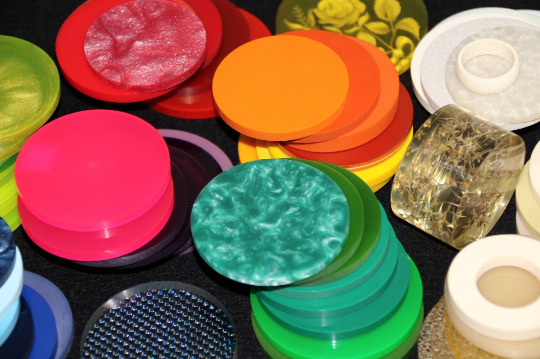
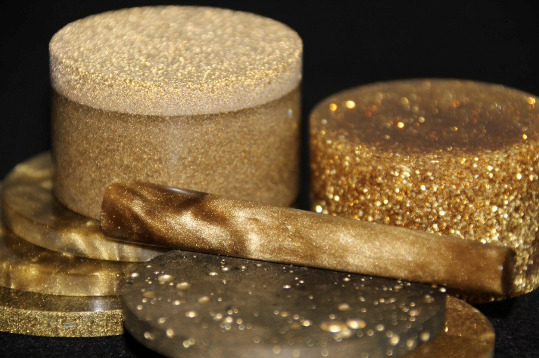
Innovation: itr2®-Metal bonding agent
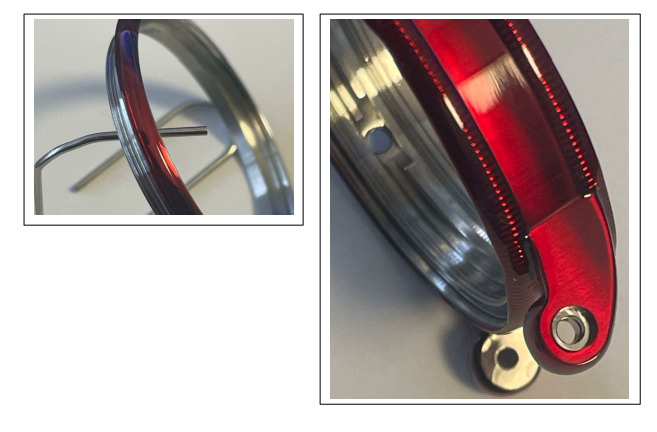
Unveiled at EPHJ 2024, this new product is the result of 24 months of R&D! The chemical bonding solution between itr2® and metal will revolutionise this field, which until now has relied solely on mechanical bonding solutions to bond a composite resin to a metal. Special shapes had to be created in the metal inserts to allow the composite resin to infiltrate, creating a bond between the resin and the metal.
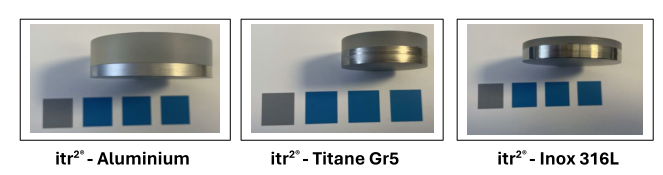
The new solution is totally transparent and leaves no visual traces on the metal surface. The result is a two-component, one-piece material suitable for machining, bead-blasting, satin-finishing or mirror-polishing. The invisible bond perfectly reveals the surface and shapes of the metal. Just the thing to get creative juices flowing! Ten years on from the launch of itr2®, its evolving concept for developing composite materials that are innovative, functional and aesthetically pleasing, Injector continues to set new standards.
www.injector.ch
by Joël A. Grandjean / JSH News 1876